Comprehensive Guide to Inventory in Accounting
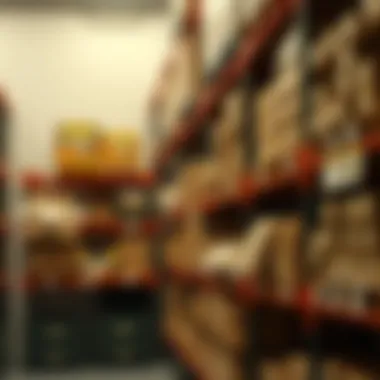
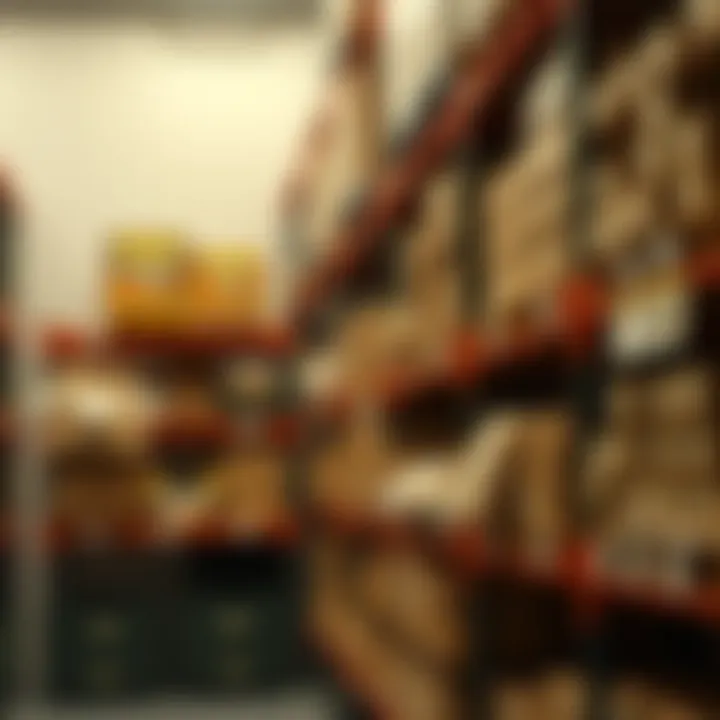
Intro
In today’s dynamic business landscape, inventory stands as a cornerstone in accounting practices. It transcends mere products on a shelf; inventory signifies the lifeblood of many organizations. Understanding its nuances not only aids in tracking what a business owns but also influences decision-making and operational success.
This article unfolds the multi-faceted nature of inventory in financial accounting. It encompasses definitions, various types, valuation methods, and the impact on financial statements, providing a holistic view crucial for anyone interested in financial management or investment strategies.
As we navigate through these topics, it’s evident that managing inventory goes beyond following accounting principles — it’s about strategies that keep the enterprise afloat. This comprehension can serve as an effective tool for both seasoned financial enthusiasts and budding investors, generating insights that empower sound decision-making and strategic planning.
Defining Inventory in Accounting
In the realm of accounting, understanding inventory is like grasping the lifeblood of any business. Inventory is not just a number on a balance sheet; it embodies the products and materials integral to an enterprise’s operations. Its accurate definition is fundamental as it sets the stage for strategic decision-making and financial assessments. Knowing what inventory entails allows businesses to align their resources effectively and optimize their profitability.
Basic Inventory Concepts
Grasping the basics of inventory is crucial for anyone involved in accounting or business management. At its core, inventory refers to the goods and materials a company holds for sale, production, or use in its operations. This can be broken down into three main categories: raw materials, work in progress, and finished goods. Here are some key terms to keep in mind:
- Raw Materials: These are the basic components used in the manufacturing of products. Think of a bakery where flour, sugar, and eggs are raw materials waiting to be transformed into cakes or pastries.
- Work in Progress (WIP): This represents items that are being manufactured but are not yet complete. In the context of the same bakery, a half-baked cake would fall under this category.
- Finished Goods: Once products are complete and ready for sale, they fall into this group. For the bakery, this would be the cakes displayed for customers.
Understanding these terms and how these components translate into the balance sheet is essential for gauging a company’s health. For businesses, effectively managing inventory enables them to minimize costs and maximize sales opportunities. Just like an artist with an organized toolbox, proper inventory organization ensures that every piece is accounted for and ready when inspiration strikes.
The Role of Inventory in Business Operations
The impact of inventory stretches beyond mere accounting—it's a strategic asset that influences every facet of a business. Inventory holds a pivotal role in operational efficiency, cost control, and customer satisfaction. When inventory levels are calibrated correctly, businesses can ensure they meet customer demands without incurring excess costs.
- Supply Chain Efficiency: An optimized inventory system can enhance supply chain performance. For instance, a construction company managing its timber supplies effectively ensures that projects continue smoothly, avoiding delays.
- Cash Flow Management: Keeping too much inventory might tie up cash that could be used elsewhere, whereas insufficient inventory can lead to missed sales opportunities. Finding the sweet spot is key.
- Customer Satisfaction: Businesses that can deliver products promptly tend to retain loyal customers. Imagine a pizza shop with fresh ingredients fully stocked during busy hours; this not only satisfies the customers but keeps the wheels of business turning smoothly.
To encapsulate, defining inventory is more than simply recognizing it as goods; it’s about appreciating its broader implications in accounting and business strategy. The efficient management of inventory can make or break a business in today’s fast-paced environments, where every decision counts.
Types of Inventory
Understanding the various types of inventory is crucial for any business. Each type serves a unique purpose in the supply chain and affects how businesses manage their resources and finances. When companies know the distinctions among the different inventory types, they can optimize stocking practices, streamline their operations, and make informed financial decisions.
Raw Materials
Raw materials constitute the foundational elements required for production. These are items that have not undergone processing and remain in their original form. For example, in a bakery, flour, sugar, and eggs are all considered raw materials. They are essential because they determine the base costs of goods produced and the quality of finished products. Companies must track inventory levels of raw materials carefully to ensure they never run short, which could lead to production delays.
Keeping a tight grip on raw materials helps businesses avoid overstocking, which could lead to excess holding costs or spoilage in cases of perishable goods.
Work in Progress
Work in progress (WIP) refers to the inventory that is still undergoing the manufacturing process. This might include partially assembled products or components that are being transformed into final goods. For instance, in a furniture factory, a sofa that is in the process of being upholstered would be classified as WIP.
The management of WIP is pivotal because it represents the investments made in production but has not yet turned into sellable items. Businesses must strike a fine balance, ensuring production processes are efficient while also reducing potential bottlenecks that could tie up resources unnecessarily.
Finished Goods
Finished goods are the end products that are ready for sale. They have completed the manufacturing process and are now in a condition to be sold or distributed. For example, in the electronics industry, a smartphone that has passed quality checks, packed, and shipped is considered a finished good.
Effectively managing inventory of finished goods is essential for meeting customer demand without overstocking. It ensures that products are readily available when customers want them, supporting sales and enhancing customer satisfaction. Moreover, businesses must also consider trends, seasons, and customer preferences when managing this inventory type to avoid any needless wastage or stockouts.
Maintenance, Repair, and Operating Supplies
Maintenance, repair, and operating supplies, often abbreviated as MRO, are essential components that keep production going smoothly but are not part of the final product itself. Examples include tools, lubricants, gloves, and screws—all vital for operational efficiency but not sold directly to consumers.
Keeping track of MRO inventory can sometimes be overlooked, yet it plays a critical role in ensuring that production facilities function effortlessly. An unexpected breakdown due to a missing tool can lead to significant downtime, affecting overall productivity and costs.
"In the grand scheme of things, managing all types of inventory logically and effectively is like rubbing two sticks together to create fire—neglect it, and you may end up stranded in the dark!"
Inventory Valuation Methods
Inventory valuation methods are essential techniques in accounting that determine the value of a company’s inventory on its financial statements. Understanding these methods is not only pivotal for accurate reporting, but also critical for strategic decision-making. The methods chosen can significantly affect a business's reported profits, tax obligations, and ultimately its cash flow. Thus, businesses need to approach these methods with care, considering how they align with their operational strategies and market conditions.
First-In-First-Out (FIFO)
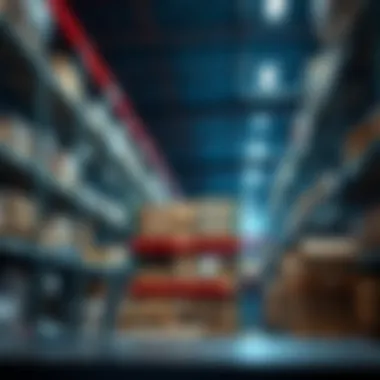
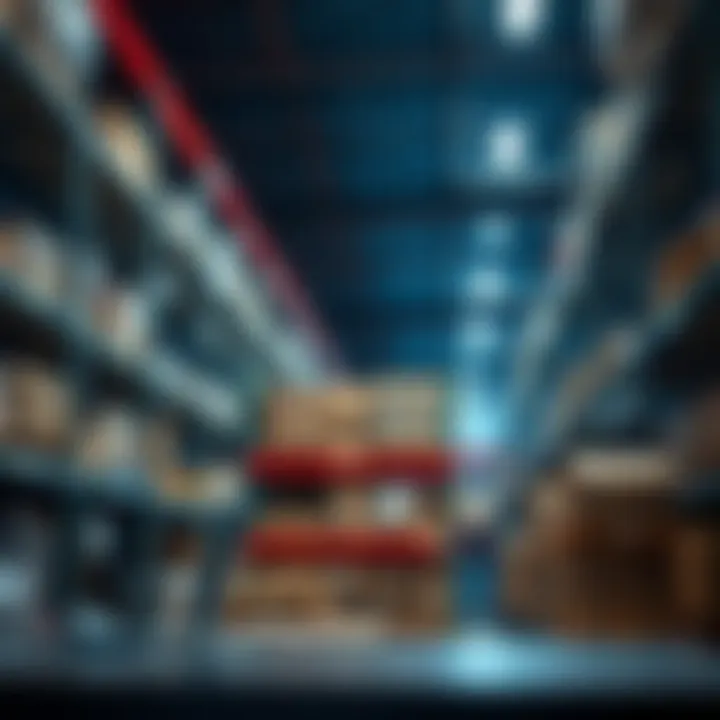
The First-In-First-Out, or FIFO method, operates on the premise that the oldest inventory items are sold first. This method is particularly useful in industries where products have a limited shelf life, such as food or pharmaceuticals. By utilizing FIFO, companies can ensure they are selling the older inventory before it becomes outdated, which helps in preventing spoilage and wastage.
From a financial perspective, FIFO tends to provide a more favorable view of profits when prices are rising, as older, cheaper costs are matched against current revenues. This can lead to higher net income on the income statement during inflationary periods. However, it's worth noting that as income tax is based on profits, this can also result in higher tax liabilities for the organization.
Last-In-First-Out (LIFO)
Conversely, Last-In-First-Out (LIFO) suggests that the most recently acquired inventory items are sold first. This method can be beneficial for businesses operating in inflationary environments, as it allows them to match higher costs against revenues, potentially lowering their taxable income and providing tax advantages.
That being said, LIFO may not reflect the actual flow of goods—especially in commodity sectors where older inventory is often consumed first. Because of its implications on profit reporting, LIFO is not allowed under International Financial Reporting Standards (IFRS), which could limit its applicability in global markets. Understanding when to apply LIFO could be a game-changer depending on the economic landscape.
Weighted Average Cost
The Weighted Average Cost method calculates inventory valuation by averaging the costs of all inventory items available for sale during the period. This method smooths out price fluctuations over the accounting period, which can be advantageous for businesses facing volatile prices. As a result, it offers a clear picture of cost over time.
Using the weighted average method helps simplify bookkeeping as one average cost is applied to each unit sold, leading to less variability in profit reporting. However, in times of rising or falling costs, profits may appear less favorable when compared with FIFO or LIFO methods. Choosing the weighted average method should align with the business's operational needs and strategic goals.
"The choice of inventory valuation method can have a significant ripple effect on a company's financial outcomes. It’s not just about the numbers but also about the story those numbers tell about operations and strategy."
In sum, the method of inventory valuation a company selects plays a crucial role in its financial statements and operational strategies. Each of these methods—FIFO, LIFO, and Weighted Average Cost—has unique advantages and challenges, and understanding these can empower businesses to make informed decisions.
Inventory and Financial Statements
In the realm of accounting, inventory holds a significant position not just in the day-to-day management of products, but also in how it reflects on financial statements. For any business, grasping the interplay between inventory and these statements is vital for making informed decisions that influence overall profitability. Inaccurate inventory data can mislead stakeholders and could even trigger scrutiny from financial regulators. This section will dissect the impact of inventory on both the balance sheet and the income statement, honing in on the specific elements that matter most.
Impact on Balance Sheet
The balance sheet serves as a snapshot of a company's financial health at a specific point in time, and inventory plays a key role in this portrayal. Essentially, inventory is classified as a current asset, which means it can be readily converted into cash within a year. This classification is crucial because it contributes to the liquidity position of the business.
- Current Assets: Under the current assets category, inventory is one of the first items listed. This metric directly affects working capital, which is calculated as current assets minus current liabilities. An optimal inventory level ensures that a business can meet its short-term obligations without scrambling for cash.
- Valuation Methods: As discussed earlier, methodologies like FIFO or LIFO influence the valuation of inventory. Depending on the approach used, the value listed on the balance sheet will vary, thereby impacting financial ratios like the current ratio and quick ratio. This, in turn, has implications for creditworthiness.
An important consideration boils down to how effectively a business manages its inventory. If there's excessive inventory, it could indicate inefficiencies. Conversely, inventory that's too lean may suggest that the business is missing out on potential sales, impacting profitability in the long run.
Impact on Income Statement
The income statement, which summarizes revenues and expenses over a specific period, is where the effects of inventory become even more pronounced. The cost of goods sold (COGS)—calculated based on the inventory valuation methods—directly influences net income.
- Cost of Goods Sold: A higher COGS reduces gross profit, which means lesser net income for the period. Companies must pay close attention to their inventory practices to avoid inflated costs. For instance, using LIFO in times of rising prices can lead to a higher COGS, reducing taxable income but also affecting cash flow.
- Gross Profit Margin: Inventory levels also impact gross profit margins. If a company has significant write-downs due to obsolescence or spoilage, it can skew profitability metrics. Thus, maintaining accurate inventory valuation is essential not just for compliance, but for giving stakeholders a realistic view of the company's performance.
"Inventory management is the backbone of financial reporting—neglecting its accuracy can lead to the downfall of even the most promising enterprises."
In summary, understanding the connection between inventory and financial statements is not merely an exercise in accounting debits and credits. It carries with it the responsibility of ensuring that financial representations are accurate, informative, and useful for both management and external stakeholders. Proper inventory management provides insight into operational efficiencies and impacts strategic decision-making, ensuring that businesses remain agile in a competitive landscape.
The Significance of Accurate Inventory Management
Accurate inventory management is no small potatoes in the realm of accounting. It serves as the backbone of a business's operational and financial health. When inventory levels are correct, companies can streamline operations, minimize costs, and ultimately improve profitability. Missteps in this area can be downright costly, often leading to excess inventory or, worse, stockouts that can tarnish a company's reputation. Knowing what you have on hand—down to the last widget—allows businesses to plan production schedules, manage supply chains effectively, and respond to customer demand with agility.
Enhancing Operational Efficiency
When it comes to operational efficiency, accurate inventory management acts like a well-oiled machine. Businesses that harness precise inventory data can allocate resources more wisely. This includes everything from staffing levels to production timelines. Without accurate inventory records, a company risks having too much of some items and too little of others, leading to cash flow issues.
For example, consider a local bakery that is notorious for its fresh pastries. If the bakery has inaccurate inventory records, it may end up overstocking on ingredients like flour while running low on essential items like eggs. This not only disrupts production but can also lead to missed sales opportunities and wasted ingredients.
A few benefits of accurate inventory in operational efficiency include:
- Reduced Holding Costs: Less money tied up in unsold goods means more cash flow for business needs.
- Streamlined Fulfillment: Faster processing times because there is no time wasted searching for items or scrambling to balance stock levels.
- Better Supplier Relationships: Accurate tracking allows businesses to negotiate better terms by ordering based on credible data rather than estimates.
As you can see, enhancing operational efficiency is not just about saving a buck; it's about creating a seamless workflow that keeps customers coming back for more.
Supporting Strategic Decision-Making
Accurate inventory management provides a treasure trove of data that can be pivotal for strategic decision-making. From investment decisions to marketing campaigns, the insights gained from inventory data can guide organizations in myriad ways. Companies can identify trends in what products are moving off the shelves and which items are gathering dust, leading to informed choices about future purchases or even product discontinuation.
"Having the right data at the right time can mean the difference between making a profit and being in the red."
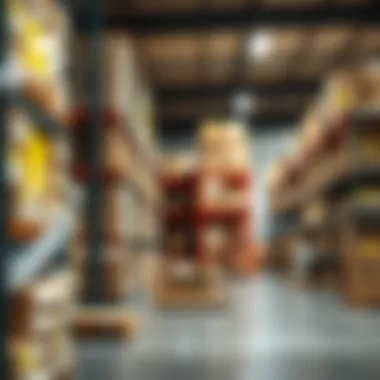
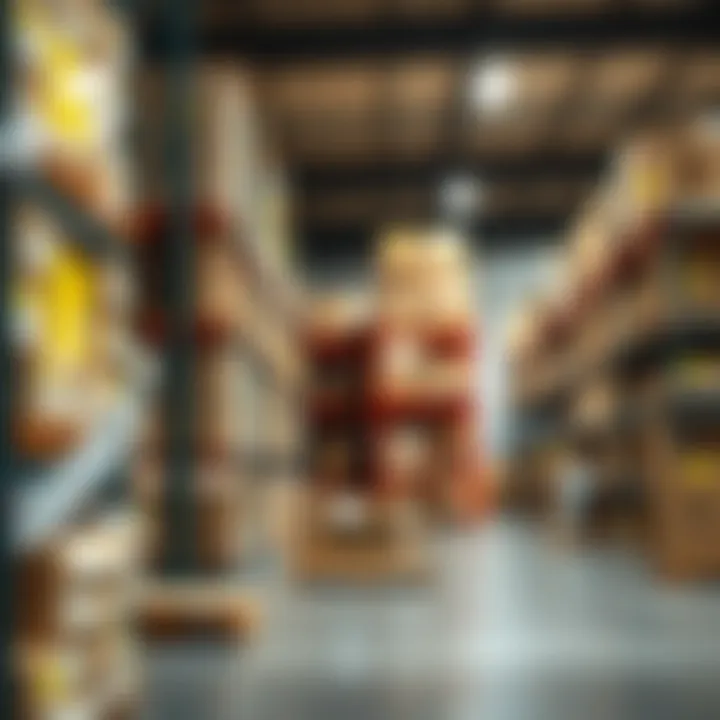
For instance, a tech company analyzing its inventory of various gadgets might discover that a particular model is flying off the shelves while another is barely moving. This information can direct the marketing team to promote the hot-selling item, while also assessing whether it makes sense to discount or rework the underperformer.
Here are some strategic decisions heavily influenced by accurate inventory management:
- Market Analysis: Understanding market demand and adapting product lines accordingly.
- Cost Control: Knowing which items have higher margins can lead businesses to prioritize those in their sales strategies.
- Long-term Planning: Accurately forecasting needs over months or years, aligning with broader business objectives.
In summary, accurate inventory management doesn’t merely support day-to-day operations; it shapes the visions and strategies that can propel a company to future success. By keeping a finger on the pulse of inventory levels, businesses can position themselves as agile competitors in today’s dynamic market.
Challenges in Inventory Management
In the realm of accounting, understanding the challenges in inventory management is crucial for maintaining a company's financial health. Accurately managing inventory not only affects a company's bottom line but also has wider implications for operational efficiency and competitiveness. Addressing these challenges can lead to enhanced decision-making and mitigate potential losses. Here, we delve into the specific elements that pose difficulties in inventory management, examining how they can impact businesses.
Obsolescence and Spoilage
One significant hurdle in inventory management is dealing with obsolescence and spoilage. As products age or market conditions shift, items may not sell as anticipated. For instance, consider a grocery store: if fresh produce isn’t sold in time, it goes bad. Conversely, technology firms often encounter obsolescence with electronics that quickly become outdated as new versions hit the market.
Effective management strategies must include timely inventory rotations and more accurate forecasting methods to minimize waste. Companies often employ techniques like the First In, First Out (FIFO) method to prevent older stock from sitting too long. Addressing spoilage not only preserves cash flow but also aligns with sustainability goals. Moreover, keeping an eye on product life cycles can help businesses avoid the pitfalls of holding onto items that lose value. Here are a few strategies to combat obsolescence and spoilage:
- Regularly review stock levels and turnover rates.
- Implement sophisticated tracking methods for perishables.
- Train staff on handling and storage techniques to extend product life.
Stockouts and Overstocks
Another common challenge is navigating stockouts and overstocks. Stockouts occur when customer demands surpass available inventory, resulting in lost sales and potential damage to a brand’s reputation. On the flip side, overstocks tie up valuable capital, leading to increased holding costs. For example, if a textile company predicts high demand for a clothing line but miscalculates, it might find itself short on popular sizes, frustrating customers eager to buy.
Managing these extremes requires a balanced approach. Businesses can utilize data analytics to better forecast demand and adjust purchase orders accordingly. This involves analyzing historical sales data and accounting for seasonality in sales patterns. A few essential measures to address these issues include:
- Use point-of-sale data to recognize purchasing trends.
- Implement order management systems that streamline replenishment processes.
- Maintain a flexible supplier network to quicken reorder times.
Complexity in Tracking and Reporting
Lastly, complexity in tracking and reporting inventory presents a significant challenge. As businesses grow, inventory systems often become convoluted. Companies may struggle to maintain accurate records across multiple locations or warehouses. This disorganization might lead to discrepancies between what’s physically on hand and what’s recorded in financial statements.
To tackle this complexity, businesses should invest in integrated inventory management solutions that allow for real-time tracking and reporting. These tools can simplify processes, providing clarity and reliability. The benefits of streamlined tracking include:
- Reduced errors in inventory counts.
- Improved operational efficiency through centralized information.
- Enhanced ability to report accurate figures in financial statements, thus building trust with investors.
"Inventory management is not a destination; it's an ongoing journey that demands constant attention and adaptation."
Technological Advancements in Inventory Management
In the ever-evolving landscape of business, technological advancements have transformed inventory management from a mundane necessity into a strategic powerhouse. The integration of technology streamlines processes, reduces human error, and enhances decision-making. For any company, whether it's a small startup or a colossal multinational corporation, embracing these technological tools isn't just a choice anymore; it's a prerequisite for maintaining competitiveness in the market.
Automation in Inventory Tracking
Automation in inventory tracking is a game-changer. By utilizing systems that automate inventory counts and updates, businesses can ensure a much higher level of accuracy.
- Real-Time Monitoring: Automated systems often employ technologies like RFID (Radio Frequency Identification) or barcode scanning. These ensure that every item can be tracked instantly, eliminating the lag associated with manual entry. If you’ve ever spent an hour trying to find where that batch of widgets went, you know how crucial this is.
- Reduction of Human Error: Mistakes in inventory can cost a business dearly. Automation significantly mitigates that risk. An automated system reduces the reliance on people, who, let's face it, are prone to overlook (or lose) the odd shipment or two.
- Cost Efficiency: By automating tracking, retailers gain efficiency, which often translates into savings. Think about how the saved hours spent on manual checks can be redirected.
With these innovations, companies aren't just maintaining their stock; they're mastering it. The investment in such technologies pays off over time, yielding richer operational insights and healthier profit margins.
Data Analytics for Inventory Optimization
Data analytics has grown into an essential component of inventory management. In an age where information drives decisions, turning raw data into actionable insights can significantly enhance the way a business approaches its inventory.
- Informed Decision-Making: Companies can now analyze consumer buying patterns with greater accuracy. By using software tools to sift through mountains of data, businesses can predict which items are likely to fly off the shelves based on trends. This foresight helps in making smarter purchases and stock levels.
- Optimizing Stock Levels: With a closer analysis of turnover rates and seasonal variations, companies can avoid being caught flat-footed during peak times. No more overstocking items that might gather dust.
- Enhanced Forecasting: Historical data on sales mixed with predictive analytics allows businesses to forecast with remarkable clarity. They might identify that a specific item tends to spike in sales every summer, for example. This level of analysis not only helps maintain optimal inventory but also supports timely replenishment.
"Data isn’t just a buzzword; it's the roadmap to efficient inventory management that every savvy business should follow."
Investing in data analytics tools is not just for the big players anymore. Small and medium-sized businesses can equally benefit from technologies that facilitate complex analysis without the need for a full-time data analyst on the payroll.
Inventory Control Methods
Inventory control methods play a crucial role in ensuring that businesses manage their stock efficiently. Without a well-structured inventory control system, companies can find themselves in a precarious position, juggling between surplus and shortage of goods. The aim is not merely to hold vast amounts of stock but to balance availability with cost efficiency. In an ever-competitive market, using these methods not only enhances customer satisfaction but also also improves the bottom line.
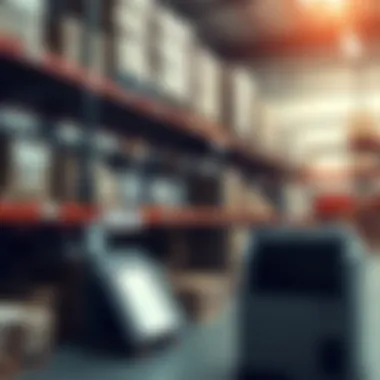
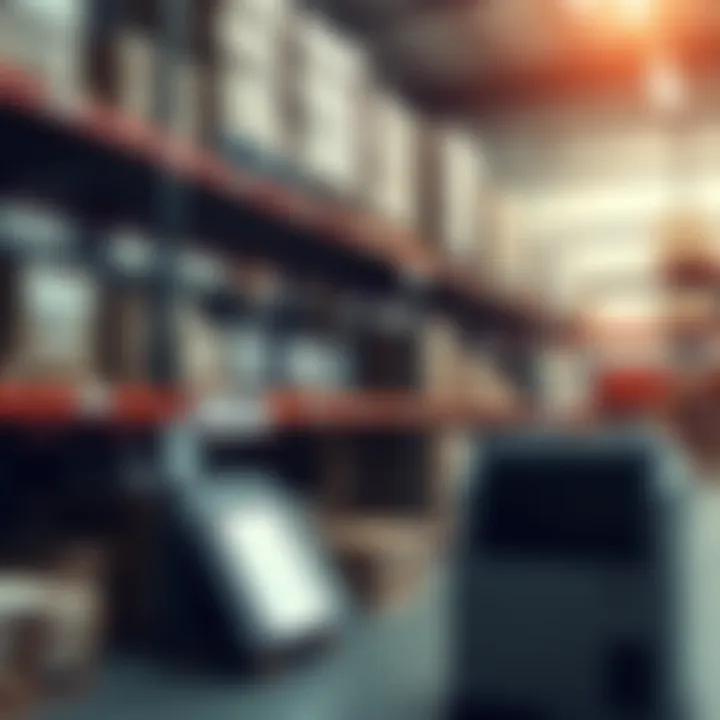
Just-In-Time (JIT) Inventory
Just-In-Time inventory management is a strategic approach that calls for the right materials to arrive at the right time in the right amount. Imagine a restaurant that only orders fresh seafood when an order is placed, instead of stocking it. This method minimizes storage costs and enables businesses to respond swiftly to market demands. There are several benefits tied to JIT:
- Reduced Storage Costs: With less inventory on hand, companies save on warehousing expenses.
- Freshness and Quality: This method ensures that products are new and not hanging around in a dusty old corner.
- Increased Efficiency: Businesses focus on a consistent flow rather than a pile of leftover stock, streamlining operations.
However, this method is not without its challenges. Supply chain disruptions can pose significant risks and may lead to missed opportunities if not managed adeptly. A hiccup somewhere in the supply chain could lead to delays that may disappoint customers.
ABC Analysis
ABC Analysis is another effective method for inventory control that categorizes stock based on its importance. It's a bit like using a grading system for your inventory. Items are classified into three categories:
- A Items: These are high-value items that make up a large portion of your inventory costs but a small percentage of total items. Think of high-end electronics.
- B Items: Moderate in value and importance; these items would hit the mid-range of the inventory spectrum, like clothing or household appliances.
- C Items: Low-value items but often high in quantity; these could include everyday items or small office supplies.
Using ABC Analysis allows businesses to focus their efforts where they count most. Activities like ordering and tracking can be tailored to the specific needs of each category. By keeping a keen eye on A items, for example, companies ensure that stock depletion doesn't occur, which could impair operations.
To sum it up, applying effective inventory control methods like Just-In-Time and ABC Analysis provides your business with tools necessary to maximize operational efficiency while minimizing waste. Strategies grounded in well-evaluated data create an environment where informed decisions can flourish, ultimately leading to a significant improvement in overall performance.
"Being organized is a skill that can save both time and money. When it comes to inventory, control methods can be a game changer."
Inventory Auditing Practices
Inventory auditing practices are essential for ensuring the accuracy of inventory records, which in turn affects a company’s financial standing and operational efficiency. These practices help in identifying discrepancies, losses, and the overall health of inventory management. Well-executed inventory audits can lead to informed decision-making, ultimately contributing to profitability and sustainability for businesses.
When it comes to managing inventory, neglecting regular audits can lead companies down a slippery slope. Without consistent checks, businesses risk overstocking or running out of essential items, which can create unnecessary expenses or lost sales. Effective auditing measures not only focus on physical counts of inventory but also involve strategic practices that enhance accountability and refine processes.
Benefits of Regular Inventory Audits:
- Accuracy of Financial Statements: A regular audit ensures that inventory levels are correctly reflected in financial statements, which is crucial for investors and stakeholders.
- Enhanced Decision-Making: Knowledge of inventory status allows managers to make data-driven decisions, optimizing stock levels and minimizing waste.
- Loss Prevention: Audits can identify discrepancies that may arise from theft, damage, or mismanagement of inventory.
- Operational Efficiency: By streamlining inventory processes through audits, companies can reduce excess holding costs and improve turnaround times.
Engaging in effective auditing practices is no small feat; it really requires a well-thought-out approach that balances thoroughness with efficiency. Below are the two prominent methods of auditing inventory that many companies adopt:
Physical Counts
Physical counts involve the direct counting of actual inventory on hand. This method is straightforward but demands meticulous planning. Generally, companies will conduct a full physical count at least once a year to validate inventory levels against recorded amounts in their systems.
The main steps in physical counting include:
- Preparation: Inform staff, and organize inventory area to minimize disruptions during the counting process.
- Counting: Teams of employees methodically account for all items, marking them off lists or using software to record quantities.
- Reconciliation: Compare physical counts with inventory records to identify any variances.
- Adjustment: Update inventory records to reflect accurate counts and investigate any significant differences.
While this method is effective in uncovering inaccuracies, it can be time-consuming and may require halting normal operations during the count.
Cycle Counting
Cycle counting is a more dynamic approach compared to physical counts. This method involves counting a portion of the inventory on a regular basis, instead of doing an all-encompassing count at once. Using cycle counting helps spread out the workload and minimize disruptions in operations.
Key features of cycle counting include:
- Regular Intervals: Counts are scheduled throughout the year, with different sections of inventory being counted at different times.
- Focus on High-Value Items: Businesses often prioritize counting items that have a higher financial impact to ensure accuracy where it matters most.
- Empowerment of Staff: Cycle counting allows employees to take ownership of the counting process, encouraging a culture of diligence and accountability.
Adopting either physical counts or cycle counting largely depends on the nature of the business, size, and inventory complexity. However, both methods share the common goal of fostering reliable inventory records that contribute to the overall success of financial management.
Future Trends in Inventory Accounting
In today's dynamic business landscape, understanding the future trends in inventory accounting is pivotal for companies aiming to maintain a competitive edge. As commerce evolves, especially with the acceleration brought about by digital transformation, the ways in which inventory is managed and accounted for are undergoing significant changes. This section dives into noteworthy trends that shape inventory accounting practices, emphasizing the growing interdependencies between technology, sustainability, and consumer behavior.
Impact of E-commerce on Inventory Practices
The rise of e-commerce has undeniably altered traditional inventory practices. Businesses are now compelled to reevaluate how they handle inventory due to increased online purchasing behaviors. Here are some key impacts:
- Real-time Inventory Management: Online platforms necessitate a transition to real-time inventory tracking. Companies are investing in sophisticated software that allows them to monitor stock levels instantly, minimizing the risk of overselling or stock shortages.
- Omnichannel Fulfillment Strategies: As customers expect seamless transactions across platforms, businesses must integrate their inventory across physical stores and online marketplaces. This consolidation ensures a fluid customer experience, regardless of how they choose to shop.
- Data-Driven Decision Making: E-commerce provides copious amounts of data on buying patterns. Companies are increasingly leveraging this information to forecast demand and adjust inventory levels accordingly, often employing algorithms that adapt to real-time market conditions.
These shifts not only enhance customer satisfaction but also minimize excess inventory costs, leading to greater overall efficiency.
Sustainability Considerations in Inventory Management
With growing awareness about environmental impact, sustainability is becoming a cornerstone of inventory management practices. Stakeholders now recognize that adopting sustainable methods is not merely an ethical choice but also a strategic business decision. Key aspects include:
- Minimized Waste: Companies are adopting just-in-time inventory practices to reduce waste through careful tracking and planning. This approach not only curtails excess stock but also leads to more efficient resource use.
- Eco-friendly Packaging: There's a push towards sustainable packaging solutions, ensuring that products are not only delivered efficiently but also in a manner that minimizes environmental harm.
- Carbon Footprint Assessment: Businesses are beginning to consider the carbon footprint associated with their supply chain and logistics. Understanding the environmental impact of transportation choices, for instance, can lead to more sustainable practices.
"Sustainability doesn't just mean being socially responsible; it's about future-proofing your business against evolving market demands."